views
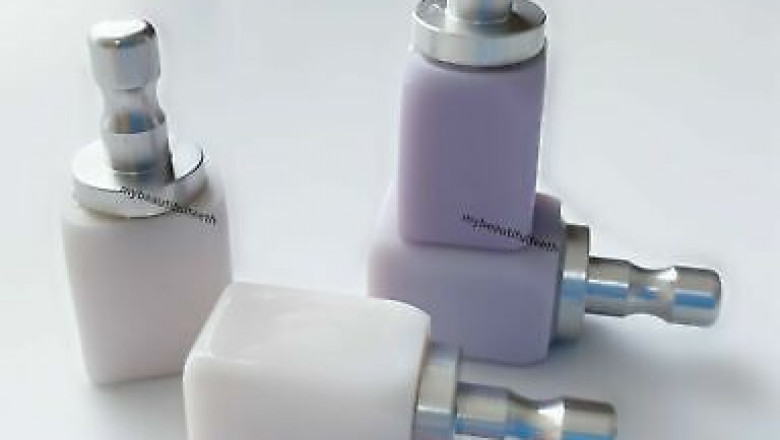
How glass-ceramic blocks for CAD/CAM applications are manufactured?
Glass-ceramic blocks are used in a wide range of industries, from aerospace and automotive manufacturing to medical devices and consumer goods. In this article, we'll look at the different ways these blocks are manufactured, and what factors go into deciding which method to use.
Glass-ceramic blocks are manufactured by a process called “melt spinning.”
Glass-ceramic blocks are made from a mixture of glass and ceramic. The glass is melted and then spun at high speeds to create the blocks.
The blocks are then cooled and shaped. Additonally, you can check also the dental zirconia block which is a metal free material.
image source: https://www.pinterest.ph
The molten glass is spun at high speeds to create the desired block shape
Block production begins with a molten glass bath
The bath is continuously fed by jets of gas
The spinning bath creates a centrifugal force that pushes the molten glass towards the center
The outside of the bath is cooled while the inside continues to spin
As the outside becomes cool, it solidifies around the center
The centrifugal force separates the blocks from the rest of the bath
The glass-ceramic blocks are then cooled and polished
The glass-ceramic blocks are then cooled and polished. After the blocks have been cooled, they are cut into desired shapes. Next, the blocks are polished to a high shine.
You may check other products that we have such as high translucent zirconia, zirconia dental material, full zirconia, cad cam, multilayer Zirconia and more. They are in high quality so you are sure that they are reliable.
image source: https://www.pinterest.ph
Conclusion
The glass-ceramic blocks for CAD/CAM applications are manufactured in a very precise way. The first step is to create a master model of the part that you want to manufacture. This model is used as a template to produce hundreds, or even thousands, of copies that are then individually cut and polished. By following these precise steps, it is possible to obtain blocks of perfect quality every time.
Because they combine great physical and chemical qualities such outstanding esthetics, translucency, low heat conductivity, appropriate strength, biocompatibility, wear resistance, and chemical durability, dental glass-ceramics are very appealing to dentists and patients. Through chemical composition alteration and manufacturing process optimization, initiatives to create glass-ceramics with greater strength have never stopped. One of the well-founded methods for reinforcing glass-ceramic is dispersion strengthening. Leucite is one of the most effective particle fillers utilized in dental glass-ceramics.