views
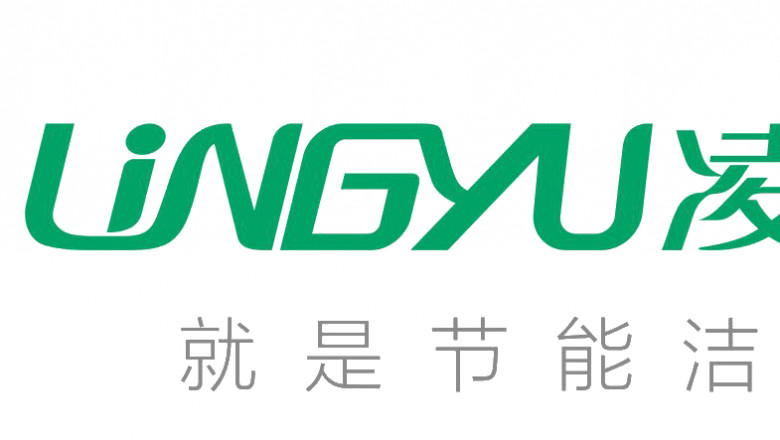
1.Composition of compressed air system
The compressed air system is composed of three parts: the air source, the pipe network and the end equipment of the air consumption. Among them, the air source is generally an air compressor station. It contains air compressor, compressed air dryer, air storage tank and filter, etc. The schematic diagram of the compressed air system is as follows.
2. How a compressed air system works?
Let's take a look at the functions of each device in the compressed air system.
(1) Air compressor
At present, most of the air compressors commonly used in industrial and mining enterprises are twin-screw type. The air compressor is mainly composed of the following systems: air flow system, lubricating oil flow system, cooling system, safety protection system, control system and electrical circuit. As the picture shows:
(2) Compressed air dryer
The function of the compressor air dryer is as follows: purify the compressed air discharged from the air compressor. That is, drying (water removal), filtration (oil removal, dust removal, etc.). Usually the equipment includes dryers (refrigerated air dryer, desiccant air dryer, etc.), compressed air filters, etc.
(3) Transmission pipeline network
The function of the conveying pipe network is to send the compressed air generated by the air compressor station to the air terminal using its own pressure. The conveying pipe network includes pipes, valves, instruments and filtering devices. Pipes generally use metal pipes.
(4) Air terminal system
It contains gas branch valve, gas distributor, instrument and end filter, etc. The compressed air of the pipeline enters the air-consuming equipment or system through the end.
3. Reasons for inefficient operation of compressed air systems
A large number of data show that the main cost of compressed air system is spent on operation. In its life cycle, operating expenses (electricity) account for as high as 78-92%. Therefore, how to tap the potential of energy consumption and improve energy efficiency through refined management is a topic that every enterprise must face. In this regard, it is found that the main reasons for the high energy consumption of most compressed air systems are as follows:
(1) Low equipment efficiency
Most of the air compressors deployed many years ago are low energy efficiency equipment. It is unreasonable to match with devices such as terminals. Just to meet the basic needs of production. The air compressor adjustment method is backward and there is no centralized control. When the air consumption varies randomly, the air compressor is wasted seriously due to unloading. The air consumption of the terminal equipment is unreasonable and the efficiency is low. The air supply is wasted.
(2) The air supply pressure is unreasonable
There is no hierarchical planning for supply air pressure. Instead, it simply uses high-pressure air supply plus a mechanical self-operated pressure reducing valve to meet different pressure requirements. A lot of energy is wasted on valves. In addition, when the air demand changes, the pressure of the pipe network will fluctuate randomly. In order to avoid frequent start and stop of the unit, it is necessary to set a wide range of pressure variation. This causes large fluctuations in the outlet pressure of the air compressor. It also increases the operating energy consumption of the air compressor system.
4. Reasons for wasting energy
(1) High no-load energy consumption
At present, most enterprise compressors are single N cubic. The compressor starts and stops only N or multiples of N. The start and stop of air compressor equipment relies on manual management.
Especially when the air load changes frequently, the system cannot respond quickly. Fine-tuning of compressor displacement is also not possible. This forms the no-load of each air compressor in the air compressor station. The energy consumption of an air compressor at no-load is as high as 40% to 70% of its full-load operation.
(2) High energy consumption for climbing
Screw compressors have two operating modes: loading and unloading operating modes or no-load and full-load operating modes.
The loading and unloading control mode makes the pressure of the compressed air run between the minimum working pressure value and the maximum working pressure. The pressure difference is generally above 1 bar. Through theoretical calculation and actual testing, it is known that every kilogram of air compressor pressure increases energy consumption by 4-8%.
(3) Traditional management
There are two inevitable contradictions in the use and management of air compressor stations:
One is that the company has a clear assessment of the air compressor management personnel. Then there will be the habit of often not enough air pressure or the habit of opening as little as possible. It is not conducive to the normal operation of the production line. Or the pressure does not meet the requirements of the equipment, resulting in an increase in the failure of the gas terminal.
One is that there is no clear assessment of air compressor managers. This will lead to more open air compressors and high no-load energy consumption of the air compressor station. No matter what kind of management mode, the result will be increased power waste in the air compressor station. And it is not conducive to safe production.
5. How to save energy in compressed air system?
(1) Frequency conversion operation of air compressor
The main energy waste of an air compressor is unloading energy consumption (power frequency compressor). When unloading, the motor runs idly and does not produce air. This method still needs to consume 40% to 70% of the rated power in the case of no gas supply. So the waste is very serious.
In addition, when the power frequency air compressor is running at partial load, it is also prone to frequent loading and unloading. It not only wastes energy consumption, but also makes the air supply pressure fluctuate. It also fatigues the motor and compressor. ultimately affect the service life.
Therefore, the frequency conversion transformation of air compressors with low and medium loads can greatly reduce the unloading time. It greatly reduce the power consumption of unloading. For laser cutting industry, it can use the PM VSD screw compressor with dryer.
(2) Dryer energy saving
For a normal refrigerated air dryer, it consumes electricity but not air. Its power consumption accounts for about 5% of the system power consumption. Generally, it is rarely involved in the process of energy-saving renovation. Unless the equipment is old and performs poorly, consider replacing it with high-efficiency equipment.
The desiccant dryer consumes electricity and air. The air consumption of the no-heat regeneration type and the micro-heat regeneration type is above 10%. It's a huge waste of energy. It is recommended to use a zero air consumption desiccant dryer instead.
(3) Pipeline energy saving
Pipeline energy savings come from two parts:
One is to reduce pipeline pressure loss. By reducing the exhaust pressure of the air pressure, the air power consumption is reduced. Under normal circumstances, when the exhaust pressure is reduced by 0.1MPa, the air compressor can save energy by 6% to 7%;
The second is to prevent leakage of the pipe network. Pipe network leaks are common in older pipe networks. In terms of leakage, the leakage in the factory usually accounts for 10% to 30% of the air supply. And poorly managed factories can even be as high as 50%. Sometimes there are 20,000 leaks in a car assembly shop. Among them, more than 90% of the leakage comes from the aging or damage of the parts in use.
Worse still, site managers far underestimated the damage caused by the leak. Taking a 1mm diameter pipe corrosion hole as an example, under the working pressure of 0.7MPa, the wasted electricity bill is about 4,000 yuan a year.
Therefore, it is recommended to replace the old carbon steel pipes with aluminum alloy pipes in the process of energy saving reform.