views
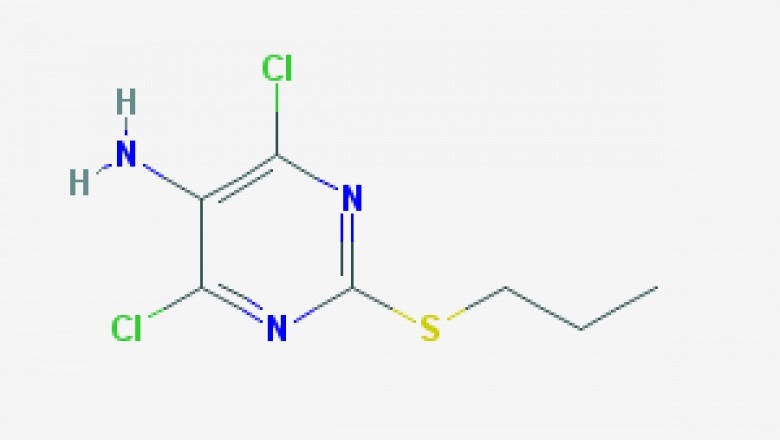
help chemical manufacturer transform operations and decrease costs
With a new and qualified partner, we can take a new look at the seemingly unsolvable challenges and help the global chemical manufacturer transform its operation mode and reduce costs.
Challenge
A $5 million global chemical manufacturer encountered Microsoft Dynamics Performance Issues in its initial Dynamics AX implementation and needed to help determine how to move forward for additional functionality. But that's just part of the story. The company is also trying to solve an unresolved problem that warehouse scanners do not assign the right code to the right products, thus providing an inaccurate view of inventory.
Because the vendor performing the initial dynamic implementation could not diagnose the problem, the warehouse staff had to manually enter all the data. This not only introduces human error, but also reduces production speed, increases completion time, and adversely affects sales orders and purchase / receipt. As they face more and more challenges and recently adopt fusion alliance as their new dynamic support partner, the company seeks answers and results from our team.
Solution
Our customers asked us to evaluate their Dynamics AX system, add features that are not available in the current version of Dynamics AX, and address performance and scanner issues. Based on their needs, our support team recommends the Dynamics AX Cu 13 update.
As part of the update, we fixed integration with third-party software, added additional custom code as needed, and addressed performance issues
Our customers have a variety of partners, so we work with our customers and their partners to successfully complete this work
In the process of this integration work, we are able to identify and fix the causes that weaken the scanners and inventory problems. The problem is inventory size, which is the driving force. Everything in the dynamic depends on the size of the inventory to perform account reconciliations, cost estimates, and accurately reflect inventory quantities. We coordinate with the customer's sales, purchasing and production teams to correct inventory accuracy.
After that, warehouse workers were able to continue using scanners, and the domino effect of positive results occurred. Productivity and warehouse activities have increased, and one process after another has become more efficient, including purchasing reception, production selection, production storage, inventory movement, inventory transfer to other warehouses, and delivery of products to customers.
With the successful installation of the update and the identification and resolution of other issues, we will continue to correct the impact of scanner issues and provide additional assistance as part of the ongoing support contract.