views
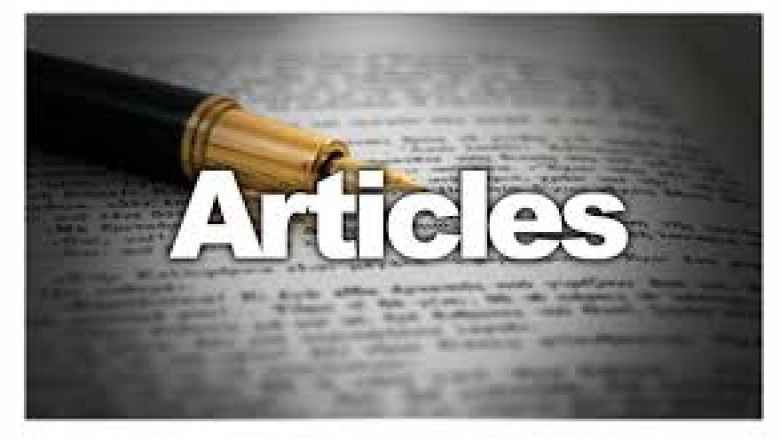
The Benefits of Kaizen
Kaizen in manufacturing is a process used to improve productivity by reducing costs and time. It also boosts employee morale and helps companies focus on their clients. The process uses a quality management system to encourage long-term improvement and create short-term excitement through celebration events. Kaizen is popularized by companies like Lockheed Martin, which has used it to improve inventory and delivery time and reduce manufacturing costs.
PDCA
For countries other than Japan, Kaizen is a relatively new concept in manufacturing. The Thai government requested that Japan provide technical support to help promote the country's productivity movement. This initiative, known as the Thailand Productivity Development Project, ran from 1994 to 2001. The Thailand Productivity Institute and Management Development and Productivity Center implemented the project. The concept of Kaizen was introduced to Thai manufacturing companies in the 1990s, even though it was only recently promoted by the Thai government.
Kaizen is the art of continuous improvement. It begins with the generation of data that is then used to create a new plan and compared to the original one. Next, analyze the results to determine what needs to change. If the results are not as expected, the process can be repeated with more data to determine if the plan is working. After analyzing the results, a new plan is developed and implemented. This process is repeated, and each test results are compared to the original plan.
Quality circles
Kaizen quality circles are a method of problem-solving that involves a team of people. Although they are not Six Sigma processes, they have the same goal: to foster collaboration, increase employee engagement, and improve problem-solving skills. Quality circles are usually applied to large groups of small projects, in order to meet a company's goals and objectives.
Each company implements quality circles differently, but the goal remains the same: to improve quality and reduce costs. This method is a form of management by empowerment. Each member of the quality circles has the power to make small decisions for themselves if necessary. For example, a quality circle may unilaterally decide to bring in employees an hour earlier than normal or make small changes to production. The goal is to make everyone's job easier and maintain the quality of the product/service.
Self-directed teams
Self-directed teams have a proven track record of improving production. Teams that work on their own have the advantage of being close to the Barcode Generator
and know their machines better than anyone else. As a result, they are able to make faster decisions, such as stopping a line when there is a quality issue. This means that they can fix the problem without needing a supervisor's help.
Kaizen involves every employee in a company and encourages them to take ownership for their actions. Kaizen encourages collaboration and productivity, as well as quality and productivity. Employees work more efficiently and effectively when they act according to common values and practices. In addition, kaizen professionals focus on reducing waste.
Measurement
One of the most important elements of the kaizen process is measurement. Teams collect data to determine if the improvement is successful before implementing it. This measurement allows them to determine if the improvement was successful or not. In addition, it gives them a baseline against which to measure future improvement efforts.
The concept of Kaizen can be applied to any type of business. Even individuals can practice this concept. Many companies, such as Lockheed Martin, have used it to cut costs, improve inventory management, and improve delivery time. Kaizen must be committed from the top to succeed.
The Japanese have embraced the Kaizen method for many years, and it is now gaining ground in the West. This method emphasizes the systematic implementation of small changes to improve the overall quality of the product. Kaizen requires that changes are quantifiable and transparent. They should also be reported. This philosophy is especially helpful for manufacturing businesses.
Elimination of waste
There are many ways to reduce waste in manufacturing processes. Some of these methods include process monitoring and quality control improvements. Some involve exchanging waste materials for raw materials that are used in other processes. This method of managing waste can help you save money on packaging by using less material. Reducing waste can ultimately improve the profitability of the industry and the environment.
One type of waste is known as people waste. People waste is when people don't use their skills and knowledge to the fullest extent. This waste can be a huge source of problems in a company. Training employees can help eliminate human waste and improve productivity.