views
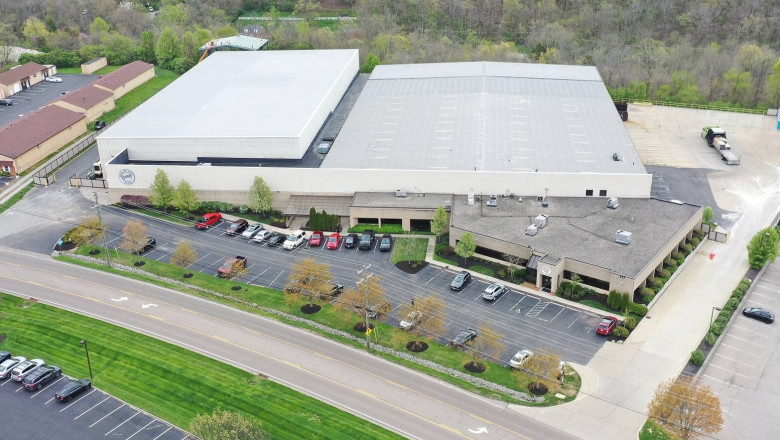
Satco, Inc. opens $10 million air cargo safety research center in Ohio
The safety and innovation of the air cargo industry impacts everyone from the pilots flying the planes, the passengers they carry, and the communities they fly over. That understanding is why Satco, Inc. made a $10 million investment culminating in the recent opening of the world's first manufacturer-owned Air Cargo Safety Research Center (ARC) in Miami Township, Ohio. The Satco ARC facility places an emphasis on optimizing the manufacturing process and safety of unit load devices (ULDs), ultimately increasing the safety of air cargo transportation.
"Our goal has always been to provide world-class, safe products that airlines, cargo, and freight companies can trust to protect their employees, assets, and the general public," said Mike Proctor, President, and CEO of Satco. "This new facility houses state-of-the-art manufacturing equipment and increases our testing capabilities, providing the space we need to continue pushing innovation to move the industry forward."
With the massive increase of products using Lithium-ion batteries, the risk of fire in cargo carried on aircrafts has become more prominent, which is why a focus point of the Satco ARC facility is the fire safety test facility or burn lab. Satco is the only ULD manufacturer with its own fire safety test facility, which is one of only a handful of testing facilities in the country. The lab is a 50' by 60' room with 36' ceilings. During a test, a controlled fire is set inside a ULD within the lab. The facility is monitored by 12 thermal imaging and HD video cameras and multiple thermal sensors to understand how a ULD is impacted by a fire during a test. The tests run for a minimum of six hours and temperatures can reach 1400+°F.
The burn lab is just a component of the testing that happens in the Satco ARC facility. The facility also houses a component testing area where the parts that make up a ULD can be tested for fire resistance and safety. This ensures every part of the ULD is fire-resistant before a complete container is made and retested in the burn lab.
"This facility gives us even more control over the safety of our products," said Michael Howell, Senior Vice President of Operations and Maintenance Services at Satco. "We don't have to wait in line at other testing facilities because we have our own. We are able to run tests whenever we need to and can quickly evaluate our products and get them to market faster."
The Satco ARC facility's location was chosen for its proximity to a number of airports known for cargo distribution from some of the world's largest companies. This will allow Satco to meet the high product demand in the region and add to the advanced manufacturing talent already present. The facility will be home for up to 120 jobs including engineers, IT specialists, and software developers.
"At the end of the day, the Satco ARC facility allows us to ensure we are manufacturing the safest ULDs on the market," said Proctor. "It also gives us a resource to anticipate new potential fire hazards in flight and plan for them. We can't just wait for a catastrophe to happen to advance the industry; we have to be proactive," he added.